Roofs & Elevated Work Areas
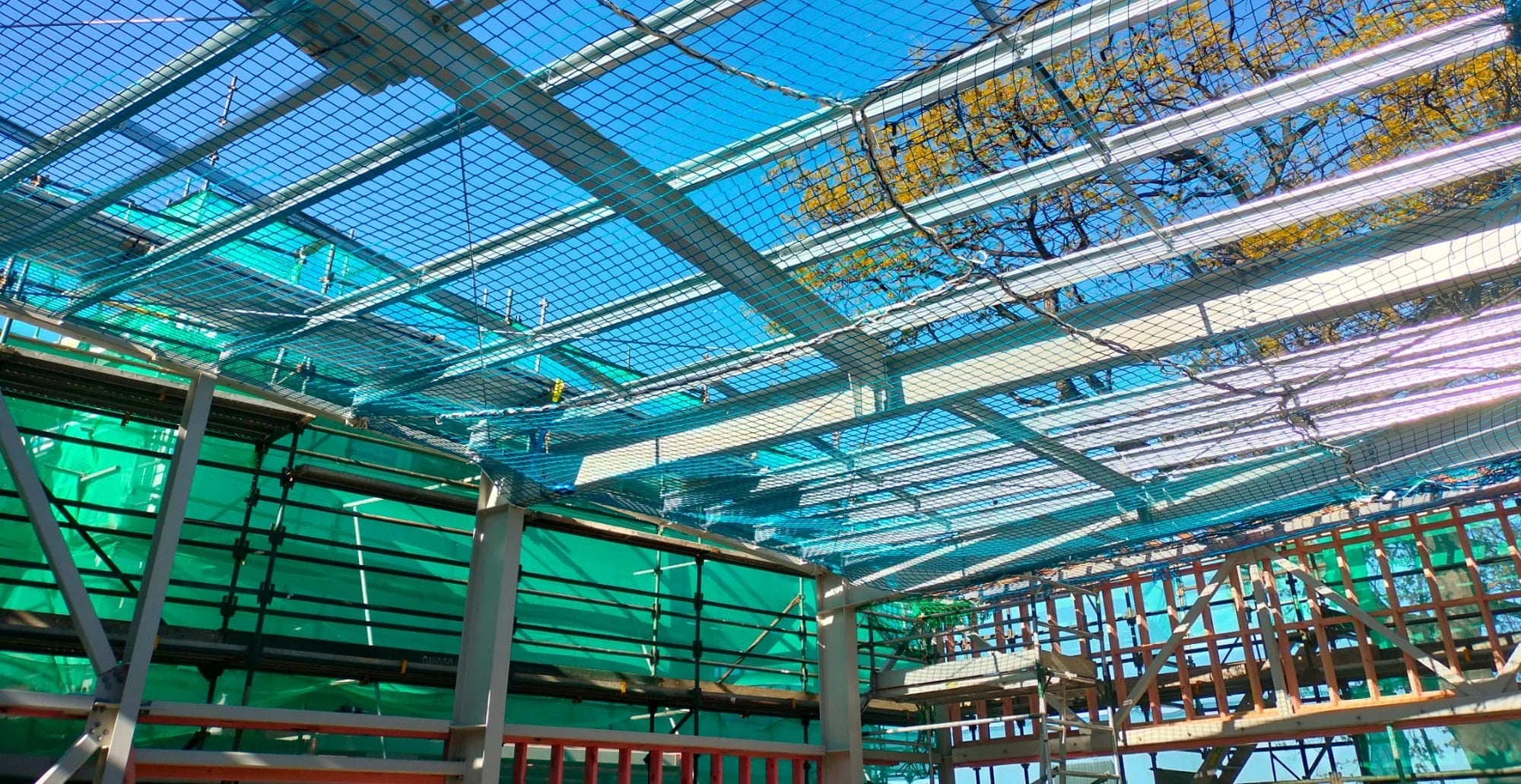
Roofs & Elevated Work Areas
Working on roofs and elevated areas requires strict safety measures to prevent accidents and injuries. Falls from height remain a leading cause of workplace incidents, underscoring the necessity of dependable safety equipment. Guardrails, safety nets, and personal fall arrest systems are essential tools, specifically designed to address the risks associated with elevated work. These solutions protect workers effectively and ensure adherence to New Zealand’s health and safety regulations. Reliable safety supplies reduce workplace liabilities, foster a safer environment, and enhance productivity by enabling workers to perform their tasks with confidence.
Our Range
Applications of Roofs & Elevated Work Area Supplies
Key Features & Advantages
Our high-quality protective films and dust mats safeguard surfaces from dust, debris, and moisture, ensuring a clean and damage-free work environment in high-risk areas such as roofs and elevated workspaces.
The pre-taped masking film and tacky dust mats feature strong adhesion, preventing movement during use while allowing for quick installation and removal without leaving sticky residues.
Designed to withstand harsh construction and industrial conditions, our protective films provide excellent resistance against water, UV exposure, and heavy foot traffic, ensuring long-lasting performance.
Our tacky dust mats effectively capture dust and dirt from footwear, reducing the spread of contaminants and maintaining a cleaner and safer workspace, particularly in enclosed or sensitive areas.
Using our protection solutions reduces the risk of surface damage, cutting down on costly repairs and clean-ups while improving work efficiency by keeping job sites organized and hazard-free.
Ideal for use in renovations, construction projects, and industrial facilities, our products adapt to different surfaces, including floors, walls, and roofing structures, providing flexible and reliable protection.
Why Use Roofs & Elevated Work Area Supplies?
Frequently Asked Questions
Active systems, like harnesses and anchors, require workers to engage with the equipment. Passive systems, such as guardrails, provide constant protection without worker involvement. Both types address fall risks but suit different scenarios and needs.
Conduct a pre-use inspection before every shift to spot visible damage or wear. Schedule thorough inspections monthly to ensure compliance and safety. Timely maintenance extends the equipment’s lifespan and prevents failures.
Most systems are made with materials designed to withstand extreme weather, including rain and UV exposure. However, regular maintenance and inspections are critical to maintaining their integrity. Severe conditions may necessitate additional precautions or replacement.s
Yes, many safety systems offer modular designs, making them adaptable to unique building layouts or project requirements. Adjustments can include variable heights, anchor point placements, and material types tailored for specific environments.
In the UK, the Health and Safety Executive (HSE) sets and enforces regulations for working at height. These include guidelines for equipment, training, and fall prevention measures to ensure legal and safety compliance.
Safety systems can last over a decade with consistent care and proper usage. Regular inspections and timely replacements of worn components are crucial to maintaining their effectiveness and compliance.